Fermenters for Catalyzing Antibiotic Production with Precision and Productivity.
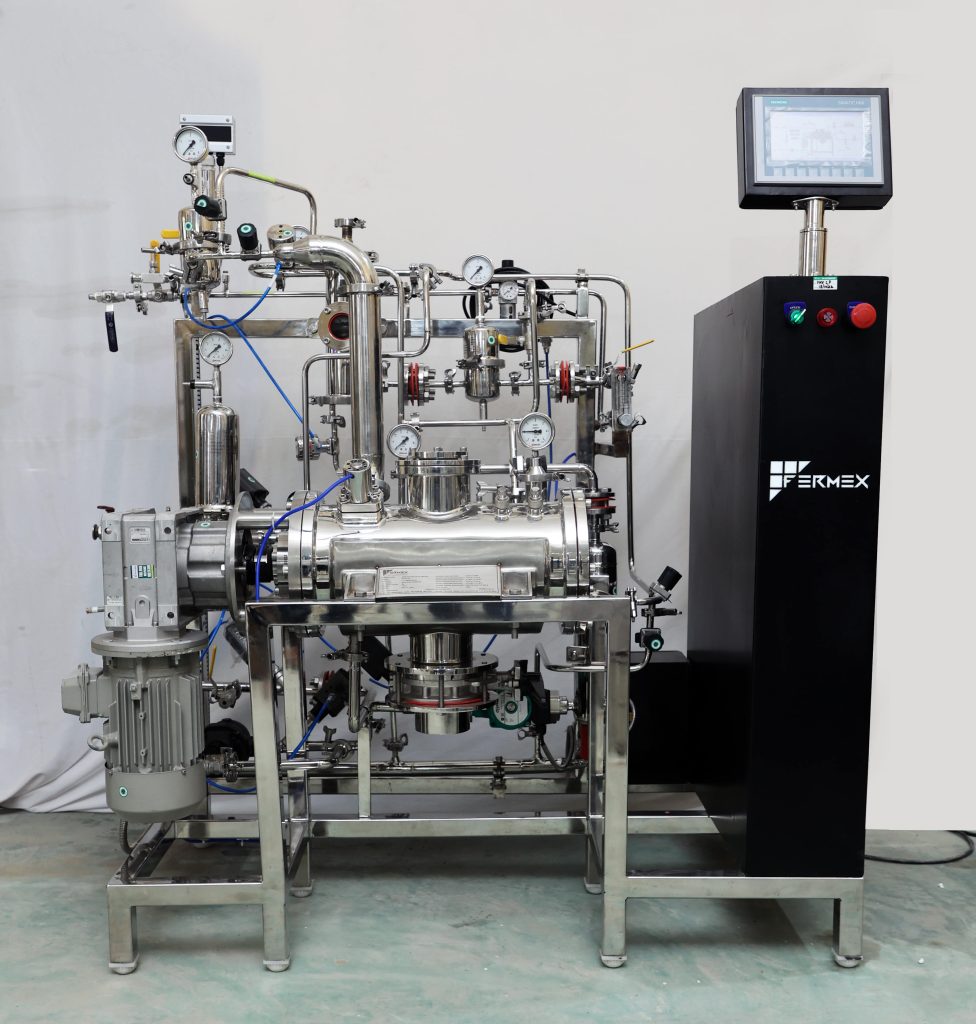
Use of Fermenter in Production of Antibiotic: –
Fermenters play a crucial role in the production of antibiotics through a process known as fermentation. Fermentation is a biotechnological process that utilizes living microorganisms, such as bacteria or fungi, to produce antibiotics. They provide an ideal environment for microorganisms to grow and produce antibiotics.
- Fermenters provide a controlled environment for large-scale antibiotic production, allowing for consistent and efficient production processes. They have revolutionized the manufacturing of antibiotics and other biotechnological products by enabling higher yields and improved quality control.
- Fermenters are specialized vessels designed to control various parameters such as temperature, pH, oxygen supply, and agitation. They enable the scaling up of the production process from small laboratory cultures to large-scale industrial production.
Key stages involved in process of making Antibiotics using Fermenters
The process of making antibiotics using fermenter involves several key stages. Here are the main steps:
1. Strain Selection: A suitable microorganism strain that has the ability to produce the desired antibiotic compound is selected. This strain is typically isolated from natural sources.
2. Inoculum Preparation: A small quantity of the selected microorganism is grown in a laboratory flask or culture medium to obtain an inoculum. This serves as a starter culture for the production process.
3. Scaling Up: The inoculum is transferred to a larger vessel called a fermenter and bioreactor. Fermenters are designed to provide optimal conditions for microbial growth and metabolite production. The size of the fermenter depends on the scale of production.
4. Fermentation Process: The fermenter provides a controlled environment for the microorganisms to grow and produce antibiotics. Parameters such as temperature, pH, oxygen supply, and agitation are closely monitored and controlled throughout the process.
5. Nutrient Supply: The fermenter is supplied with a nutrient-rich medium that contains essential ingredients for microbial growth and antibiotic production. The composition of the medium may vary depending on the specific requirements of the microorganism.
6. Antibiotic Production: As the microorganisms grow and multiply in the fermenter, they undergo metabolic processes that result in the production of the desired antibiotic compound. The fermentation process can last from days to weeks, depending on the microorganism and antibiotic being produced.
7. Harvesting and Isolation: Once the fermentation process is complete, the antibiotic-containing broth is harvested from the fermenter. The broth may contain impurities, so filtration, centrifugation, and purification techniques are used to isolate and purify the antibiotic compound.
8. Formulation and Packaging: The purified antibiotic is formulated into its final dosage form, such as tablets, capsules, or injectable. Quality control tests ensure its safety, efficacy, and stability. Finally, the antibiotic is packaged and prepared for distribution and use.


Fermex Solutions LLP manufactures fermenters that can be used for these productions.
- Glass Autoclavable Fermenter (Lab scale)
- In situ Solid State Fermenter (Industrial scale)
- In situ Solid State Fermenter (Pilot scale)
- In situ Submerged Fermenter (Industrial scale)
- In situ Submerged Fermenter (Pilot scale)
Benefits of Fermenters in the production of antibiotics
Fermenters offer several benefits in the production of antibiotics by providing a controlled and optimized environment for microbial growth and metabolite production. They enhance productivity, quality control, scalability, and resource utilization, making the antibiotic manufacturing process more efficient and effective.:
1. Controlled Environment: Fermenters provide a controlled environment for microbial growth and metabolite production. Parameters such as temperature, pH, oxygen supply, and agitation can be precisely monitored and controlled. This ensures optimal conditions for the growth of antibiotic-producing microorganisms and enhances productivity.
2. Scalability: Fermenters allow for scaling up the production of antibiotics from small laboratory cultures to large-scale industrial production. They come in various sizes, accommodating different production volumes. This scalability enables efficient and cost-effective manufacturing processes.
3. Improved Yield and Productivity: Fermenters optimize the conditions for microbial growth and metabolite production, leading to increased yield and productivity of antibiotics. The controlled environment and optimized nutrient supply enhance the growth and metabolic activity of the microorganisms, resulting in higher antibiotic production.
4. Enhanced Quality Control: Fermenters enable tight control over process parameters, ensuring consistency and reproducibility in antibiotic production. This facilitates better quality control throughout the manufacturing process, leading to antibiotics with consistent potency, purity, and efficacy.
5. Reduced Contamination Risk: Fermenters are designed with features to minimize the risk of contamination. They provide aseptic conditions and incorporate measures to prevent the entry of unwanted microorganisms or contaminants. This helps maintain the purity and integrity of the antibiotic production process.
6. Efficient Resource Utilization: Fermenters optimize the utilization of resources such as nutrients, energy, and space. The controlled environment ensures efficient utilization of nutrients by the microorganisms, reducing wastage and minimizing production costs.
7.Time Efficiency: Fermenters can accelerate the production process by providing an ideal growth environment for microorganisms. They enable rapid and efficient growth of the microorganisms, reducing the time required for antibiotic production.
